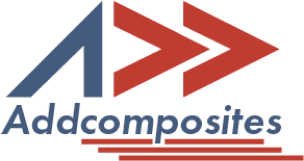
Continued from Advanced Composites Manufacturing: Beam Bending
One of the main components of a composite part is fiber. Fiber is like raw spaghetti and behaves best in tension. If you take a piece of raw spaghetti loaded in various conditions, under which type of load is it strongest? When it is bent, it snaps. When it is compressed by pushing the two ends together, it snaps. However, when we load it in tension by pulling on it, it can hold a decent load.
String, chain, wire, silk, or any other kind of strand-like material behaves the same way - it will buckle, deform, or break when bent or compressed under very small loads, yet strands can handle far greater loads when applied in tension. In any sort of engineering applications, these materials are used in ways that make use of their tensile properties. As we discussed in the Beam Bending Theory article, link above, the material above and below the neutral axis effectively behave like strands - the segments in tension have the highest impact on the beams overall strength.
As mentioned previously, the strength of a strand depends on the bonds a material makes with itself, and how that bond distributes stresses from applied loads. Yarn is made of shorter lengths of wool twisted together, so then the twists come undone, the yarn loses its strength. Similarly, a strip of fiber with resin, once it's pressed and bonded well, becomes as strong as the molecular bonds holding it all together.
This is why fibrous materials like carbon fiber, fiberglass, and Kevlar® are so valuable. Optimizing their volume percentage using ATL/AFP, these continuous fibers are known for their material properties and behavior in tension. Carbon fiber, for example, has one of the highest strength-to-weight ratios on the planet. The key to using CF to its full capabilities is to understand how a given load can distribute amongst the local fibers to apply a tensile force.
We'll catch you next time when we use the Beam Bending Theory and Fiber Strength to create fully functional Sandwich Panels, stay tuned!
Continued from Advanced Composites Manufacturing: Beam Bending
One of the main components of a composite part is fiber. Fiber is like raw spaghetti and behaves best in tension. If you take a piece of raw spaghetti loaded in various conditions, under which type of load is it strongest? When it is bent, it snaps. When it is compressed by pushing the two ends together, it snaps. However, when we load it in tension by pulling on it, it can hold a decent load.
String, chain, wire, silk, or any other kind of strand-like material behaves the same way - it will buckle, deform, or break when bent or compressed under very small loads, yet strands can handle far greater loads when applied in tension. In any sort of engineering applications, these materials are used in ways that make use of their tensile properties. As we discussed in the Beam Bending Theory article, link above, the material above and below the neutral axis effectively behave like strands - the segments in tension have the highest impact on the beams overall strength.
As mentioned previously, the strength of a strand depends on the bonds a material makes with itself, and how that bond distributes stresses from applied loads. Yarn is made of shorter lengths of wool twisted together, so then the twists come undone, the yarn loses its strength. Similarly, a strip of fiber with resin, once it's pressed and bonded well, becomes as strong as the molecular bonds holding it all together.
This is why fibrous materials like carbon fiber, fiberglass, and Kevlar® are so valuable. Optimizing their volume percentage using ATL/AFP, these continuous fibers are known for their material properties and behavior in tension. Carbon fiber, for example, has one of the highest strength-to-weight ratios on the planet. The key to using CF to its full capabilities is to understand how a given load can distribute amongst the local fibers to apply a tensile force.
We'll catch you next time when we use the Beam Bending Theory and Fiber Strength to create fully functional Sandwich Panels, stay tuned!