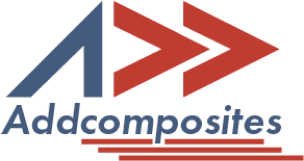
In an era where manufacturing efficiency meets environmental responsibility, advanced composite materials have emerged as the cornerstone of industrial innovation. With the potential to increase mechanical properties by up to 435% in certain applications, these materials are not just an alternative – they're driving a fundamental shift in how we approach manufacturing challenges.
The manufacturing industry stands at a crucial crossroads. Traditional materials and methods, while reliable, increasingly fall short of meeting modern demands for lightweight, durable, and sustainable solutions. Advanced composite manufacturing has risen to meet these challenges, offering unprecedented combinations of strength, flexibility, and environmental responsibility.
Consider this: when automotive manufacturers sought to reduce vehicle weight while maintaining safety standards, continuous fiber composites provided the answer. These materials have enabled weight reductions of up to 60% compared to traditional steel components, while maintaining or even improving structural integrity.
The urgency for advanced composite solutions has never been greater. Three key factors drive this need:
The evolution of composite materials represents more than just technological advancement – it's a revolution in manufacturing possibilities. From aerospace components that must withstand extreme conditions to automotive parts that enhance vehicle efficiency, composites are redefining what's possible in modern manufacturing.
This transformation is supported by cutting-edge design software and tools that enable manufacturers to optimize their use of composite materials, ensuring maximum performance while minimizing waste. The integration of artificial intelligence and machine learning in composite manufacturing processes has opened new frontiers in quality control and process optimization.
As we delve deeper into the world of advanced composite materials, we'll explore how these innovations are reshaping industries, improving products, and creating new possibilities for sustainable manufacturing. The future of manufacturing isn't just about what we make – it's about how intelligently we can combine materials and technologies to create superior solutions.
Stay tuned as we explore the specific types of composite materials, their applications, and the groundbreaking technologies that are making this revolution possible.
Advanced composite materials represent a sophisticated engineering achievement where two or more materials are combined to create something extraordinary. Unlike traditional materials, composites leverage the best properties of each component to achieve superior performance characteristics. But what makes a composite "advanced"? The answer lies in both its composition and its application potential.
Fiber-reinforced composite materials stand as the most widely recognized category. These materials combine high-strength fibers with a matrix material, creating structures that are both lightweight and remarkably strong. Key variants include:
Laminated composite materials consist of multiple layers of different materials bonded together. This structure allows for:
Matrix composites utilize a primary material (the matrix) reinforced with particles, fibers, or sheets. These materials excel in:
Beyond the traditional categories, specialized composites include:
The versatility of advanced composites has led to their adoption across numerous sectors:
The understanding of these materials continues to evolve, with new applications and improvements emerging regularly. As manufacturing technologies advance and environmental considerations become increasingly important, the role of advanced composites in industry will only grow more significant.
The journey from traditional manufacturing to today's advanced composite production represents one of the most significant technological leaps in industrial history. Understanding this evolution is crucial for appreciating the current state of the industry and its future potential. What began as largely manual processes has transformed into sophisticated, automated systems that deliver unprecedented precision and consistency.
AFP technology has revolutionized composite manufacturing by introducing a level of precision and efficiency previously unattainable. Modern AFP systems can achieve placement speeds of up to 500mm/s while maintaining exceptional accuracy. This technology has transformed how we approach complex geometries and multi-directional reinforcement, making it possible to create structures that were once considered impossible or impractical to manufacture.
The marriage of additive manufacturing and continuous fiber reinforcement has opened new possibilities in composite production. This innovative approach enables manufacturers to create complex geometries while maintaining the structural integrity provided by continuous fiber reinforcement. The technology offers unprecedented flexibility in design and rapid prototyping capabilities, allowing for quick iterations and customization that traditional manufacturing methods cannot match.
Modern filament winding has evolved far beyond its basic origins. Today's systems incorporate advanced tension control and multi-axis movement capabilities, enabling the production of complex shapes with consistent quality. This evolution has made filament winding particularly valuable in producing pressure vessels, pipes, and other cylindrical structures with exceptional strength-to-weight ratios.
The integration of digital technologies has transformed composite manufacturing from a largely mechanical process to a smart, connected operation. Digital twin technology now enables manufacturers to simulate and optimize processes before physical production begins. This capability, combined with real-time monitoring and adjustment, has dramatically improved both efficiency and quality control.
Modern manufacturing systems have become increasingly intelligent through the integration of AI and machine learning. These technologies enable:
The implementation of advanced monitoring systems has revolutionized quality control in composite manufacturing. Data-driven manufacturing now allows for continuous process optimization and quality prediction, significantly reducing waste and improving overall product consistency.
Sustainable manufacturing processes have become increasingly important in the composite industry. Modern techniques not only reduce material waste and energy consumption but also enable the use of more sustainable materials and recycling options. These environmental benefits often align with economic advantages, as improved efficiency and reduced waste translate directly to cost savings.
The future of composite manufacturing lies in the complete integration of Industry 4.0 principles. This includes the seamless connection of all manufacturing processes through IoT technology, advanced analytics, and smart factory concepts. Manufacturers are moving toward fully integrated systems that can self-optimize and adapt to changing conditions in real-time.
This evolution in manufacturing processes represents not just technological advancement, but a fundamental shift in how we approach composite material production. The convergence of advanced automation, digital technologies, and smart systems is creating new possibilities in manufacturing efficiency and capability, setting the stage for even more innovations in the years to come.
The versatility and exceptional performance characteristics of advanced composite materials have led to their adoption across a wide range of industries. From the heights of aerospace to the depths of marine applications, these materials continue to push the boundaries of what's possible in modern engineering and manufacturing.
The aerospace industry has long been at the forefront of composite material adoption. In aerospace applications, composites have revolutionized aircraft design and performance. Modern aircraft now incorporate composite materials in everything from wing structures to fuselage components, resulting in significant weight reductions while maintaining or improving structural integrity.
Automated Fiber Placement technology has become particularly crucial in aerospace manufacturing, enabling the production of complex geometries with unprecedented precision. This technology allows manufacturers to create parts with optimal fiber orientation for maximum strength while minimizing material waste. The result is aircraft components that are not only lighter but also more durable and fuel-efficient.
The automotive industry's embrace of composite materials represents a significant shift in vehicle design and manufacturing. Continuous fiber composites have become increasingly important in the automotive sector, particularly as manufacturers strive to meet stringent emissions regulations and performance requirements.
Electric vehicle manufacturers have been particularly aggressive in adopting composite materials, using them for:
The marine industry presents unique challenges that composite materials are uniquely suited to address. In shipbuilding, the combination of corrosion resistance and high strength-to-weight ratio makes composites particularly valuable. Modern shipbuilding techniques increasingly rely on composite materials for both structural and aesthetic applications.
Large marine structures benefit from the use of composite materials through:
The renewable energy sector has become a major driver of innovation in composite materials. Wind energy, in particular, has pushed the boundaries of composite manufacturing technology. Advanced composites in wind turbine applications have enabled the creation of longer, more efficient blades while maintaining structural integrity under extreme conditions.
Solar energy applications have also benefited from composite material innovations, particularly in the development of lightweight, durable mounting systems and protective components that can withstand harsh environmental conditions while maintaining optimal performance.
The role of composites in research and education cannot be overstated. Academic institutions and research facilities are continuously pushing the boundaries of what's possible with composite materials. These environments serve as crucial testing grounds for new applications and manufacturing techniques, bridging the gap between theoretical possibilities and practical applications.
Educational initiatives focusing on composite materials are preparing the next generation of engineers and designers to work with these advanced materials. This includes hands-on experience with modern manufacturing techniques and exposure to cutting-edge design principles.
The construction industry has begun to recognize the potential of advanced composites in creating more resilient and sustainable infrastructure. From bridge reinforcement to building facades, composites offer unique advantages in terms of durability, maintenance requirements, and installation efficiency. The ability to create custom solutions for specific structural challenges has made composites particularly valuable in rehabilitation and upgrade projects.
Looking ahead, the applications for advanced composite materials continue to expand. As manufacturing technologies evolve and new material combinations are developed, we can expect to see even more innovative uses across these and other industries. The key to maximizing the potential of these materials lies in understanding their unique properties and applying them strategically to solve specific industry challenges.
In the rapidly evolving landscape of composite manufacturing, Addcomposites has emerged as a pioneering force, particularly in the automation of composite manufacturing. With headquarters in Espoo, Finland, and a global presence spanning from Australia to North America, the company has established itself as a leader in making composite manufacturing more accessible and efficient for the global community.
At the heart of Addcomposites' innovation lies its two primary Automated Fiber Placement (AFP) solutions. The flagship AFP-XS system represents a breakthrough in accessibility and precision. This single-tow system demonstrates remarkable versatility through its compatibility with major robot brands including Kuka, Fanuc, ABB, Kawasaki, and Yaskawa. What sets it apart is not just its technical capabilities, but its practical implementation - the system can be installed and operational within just one month.
Taking automation to the next level, the AFP-X system caters to high-volume production scenarios. This advanced system features a four-tow capability and significantly enhanced material capacity - sixteen times that of the AFP-XS. With advanced sensors for continuous production and operating speeds up to 500mm/s, it represents the pinnacle of automated composite manufacturing efficiency.
Addcomposites' software portfolio centers around two main offerings that have revolutionized composite manufacturing processes. AddPath, their strategic path planning software, has transformed how manufacturers approach AFP operations. The software integrates sophisticated features including:
Complementing this is AddPrint, designed specifically for SCF3D printing. This specialized software handles complex CAD geometry processing with remarkable 12-axis capability for intricate surface printing, opening new possibilities in composite manufacturing.
The SCF3D (Structural Continuous Fiber 3D Printing) system represents Addcomposites' vision for manufacturing flexibility. This innovative system works with both pellets and continuous reinforcement, supporting advanced materials like PA, PEEK, and PAEK with carbon or glass reinforcement. With impressive deposition speeds of up to 9kg/hr, it sets new standards in manufacturing efficiency.
The ADD Filament Winding System further expands manufacturing capabilities. This system excels in high-tension winding applications, offering multi-material support and advanced non-geodesic winding paths, making it ideal for producing complex composite structures.
Integration capabilities are centered around AddCell, a comprehensive safety cell integration package. This sophisticated system encompasses:
Safety control systems that ensure operational security Complete wiring and cable management solutions Robot installation components for seamless integration Precise base positioning and calibration tools
Addcomposites' commitment to comprehensive solutions extends to their accessories line. Their offerings include specialized materials for AFP and SCF3D systems, precision-engineered compaction rollers, and advanced monitoring equipment. These components are designed to optimize system performance and ensure consistent, high-quality output.
What truly sets Addcomposites apart is their holistic approach to composite manufacturing automation. Their solutions have found applications across diverse industries, from aerospace and aviation to automotive and renewable energy sectors. The modular design philosophy, coupled with minimal moving parts and user-friendly operation, has made advanced composite manufacturing accessible to a broader range of manufacturers.
The future of composites manufacturing under Addcomposites' leadership continues to evolve. Their focus on plug-and-play solutions, comprehensive training programs, and global support infrastructure ensures that advanced composite manufacturing technology remains accessible while pushing the boundaries of what's possible in the field.
Through continuous innovation and a deep understanding of industry needs, Addcomposites continues to break down barriers in composite manufacturing, making advanced technology accessible to manufacturers of all sizes while maintaining the highest standards of quality and efficiency.
The future of advanced composite materials stands at an exciting crossroads, where technological innovation meets growing industrial demands. As we look ahead, several key trends and developments are shaping the trajectory of this dynamic field.
The shift towards intelligent manufacturing represents one of the most significant developments in composite materials production. Artificial intelligence and machine learning are no longer just buzzwords but are becoming integral tools in optimizing manufacturing processes. AI-driven systems are increasingly capable of predicting material behavior, identifying potential defects before they occur, and automatically adjusting processing parameters for optimal results.
Environmental considerations are driving innovation in composite materials like never before. The push for sustainable composites has led to groundbreaking developments in recyclable materials and manufacturing processes. Manufacturers are exploring bio-based composites and developing more efficient recycling methods for existing materials. This focus on sustainability isn't just environmentally conscious - it's becoming a crucial factor in meeting regulatory requirements and consumer demands.
Digital twin technology is revolutionizing how we approach composite manufacturing. These virtual replicas of physical manufacturing processes enable:
The application landscape for composite materials continues to expand into new territories. Large-scale additive manufacturing with continuous fiber reinforcement is opening up possibilities for architectural-scale applications. In the automotive sector, the evolution of electric vehicles is driving demand for innovative composite solutions that combine lightweight properties with high performance.
The next generation of composite materials is being developed at the molecular level. Research into new fiber types and matrix materials continues to push the boundaries of what's possible. These developments are focused on creating materials that are not just stronger and lighter, but also more adaptable and environmentally sustainable.
The future of manufacturing processes is trending toward greater automation and precision. Advanced manufacturing techniques are becoming more accessible to smaller manufacturers, democratizing access to high-end composite production capabilities. This democratization is driving innovation in unexpected ways, as more diverse perspectives contribute to solving manufacturing challenges.
The integration of Industry 4.0 principles is transforming composite manufacturing into a more connected and intelligent process. Machine learning algorithms are becoming increasingly sophisticated in optimizing production parameters and predicting maintenance needs. This digital transformation is enabling manufacturers to achieve higher levels of efficiency and quality while reducing waste and production costs.
The economic landscape for composite materials is evolving rapidly. While initial costs remain a consideration, the long-term benefits of composite materials - including reduced maintenance requirements, longer service life, and improved performance - are becoming more widely recognized. This shift in perspective is driving increased adoption across industries.
Current research trends indicate a strong focus on several key areas:
The autonomous manufacturing future promises to bring even more innovations, with systems capable of self-optimization and real-time adaptation to changing conditions.
As we look to the future, the composite materials industry stands poised for significant growth and innovation. The convergence of advanced manufacturing technologies, environmental consciousness, and digital transformation is creating unprecedented opportunities for development and application of these materials. The challenge now lies in harnessing these opportunities while ensuring accessibility, sustainability, and practical implementation across industries.
The evolution of advanced composite materials represents more than just a technological advancement; it marks a fundamental shift in how we approach manufacturing, sustainability, and performance in modern industry. As we've explored throughout this comprehensive overview, the impact of these materials extends far beyond their basic properties.
The manufacturing landscape has been transformed by the integration of advanced composite materials and automated manufacturing processes. From aerospace applications to automotive innovation, these materials have proven their worth in demanding environments where traditional materials fall short. The combination of strength, lightweight properties, and design flexibility has opened new possibilities across industries.
The adoption of automated manufacturing processes, particularly through solutions like those offered by Addcomposites, has democratized access to advanced composite manufacturing. This democratization is particularly significant as it enables smaller manufacturers to compete in markets previously dominated by large industrial players. The result is a more diverse and innovative industry landscape.
Sustainability in composite manufacturing has evolved from an afterthought to a central consideration. The industry's commitment to developing environmentally conscious solutions while maintaining high performance standards demonstrates the potential for technology to address both industrial and environmental needs simultaneously.
As we look to the future, several key factors will continue to drive innovation in composite materials and manufacturing:
The future success of composite materials lies not just in technological advancement, but in the collaboration between manufacturers, researchers, and end-users. The sharing of knowledge and expertise will remain crucial in driving innovation and solving complex manufacturing challenges.
Huang, X., Su, S., Xu, Z., Miao, Q., Li, W., & Wang, L. (2023). Advanced Composite Materials for Structure Strengthening and Resilience Improvement. Buildings, 13(10), 2406. https://doi.org/10.3390/buildings13102406
This blog post was developed using information from the cited academic paper and Addcomposites' technical resources. All figures, statistics, and technical specifications have been verified through these primary sources. The integration of academic research with practical industry applications provides a comprehensive view of the current state and future directions of advanced composite materials and manufacturing.