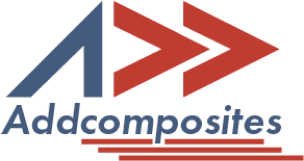
Before getting to materials and settings that determine the strength of a part produced using ATL/AFP and composites, it is important to understand the physics and theory behind different aspects that affect its strength. In this section, we cover 3 concepts that lay the groundwork for strong ATL/AFP parts.
ATL/AFP parts are rarely 100% carbon fiber, as it is beneficial for cost and material savings to reinforce only the sections that experience the most force. This is why most composite parts are constructed more like sandwiches, with the outermost sections being the composite material and the internal structure being the core.
The core's main purpose is to increase the part to the desired thickness, without building it up with expensive carbon fiber. So, does the shell thickness or core density contribute more to part strength? The answer stems from the simple beam bending theory.
The key takeaway from beam bending theory is that the top and bottom surfaces of a beam experience the most force when bent, and we can optimize the strength of a beam for its weight by only adding material at these extremes, and using as little material as possible.
Say we have a simple beam, like a bridge, supported on both sides, and weight is centered between the end supports, as shown in the following diagram.
We can abstract this model to the 3 points of contact the beam experiences - one for the weight, and two for the supports. This forms a triangle, like so, where the contact points become the vertices.
When the weight applies a force to this beam, imagine the forces distributing along with this triangular structure. The two angled segments are compressed, and the horizontal segment gets loaded in tension.
The forces are distributed along the lengths of the triangle. The magnitude of the horizontal force ultimately depends on the thickness of the beam. As the beam gets thicker while the load remains constant, the base angles of the triangle increase, reducing the resultant horizontal force on the beam. When we increase the beam, like so, we can see the angle of force applied at the supports becomes more vertical:
As these angles increase, the resultant tensile force decreases. This means a thicker beam will be able to resist the bending tensile force of the weight much easier than a thinner beam. It is common sense that a thicker beam is able to support more weight than a thinner one, and this theory explains why.
A related aspect to beam bending theory describes that the largest loads on a bent beam are applied at its extremes. A bending force applied to a beam resolves to tensile and compressive forces on either side of what is called the "neutral axis", the plane in a beam at which no load is experienced.
In this case, the material below the neutral axis is loaded in tension and above the neutral axis is loaded in compression.
This information suggests that if optimizing a beam for its strength and weight, the material has the biggest impact on the top and bottom surfaces of the part, whereas the middle endures relatively little shearing forces.
Especially in ATL/AFP, tensile loads are more important and easier to optimize for than compressive loads, because each layer of fiber behaves like a strand (more on this later).
This explains why circular and box tubing, I-beams, and T-beams are so common in construction; they save weight by only adding material where the highest stresses are experienced. A circular tube can handle loading from all sides, because no matter where force is applied from, there are two "surfaces" at the extremes.
A box can handle loads from four sides because whichever side the load is applied from has an opposite side ready to experience tension. An I-beam however, is only capable of handling extreme force from two sides, and similarly, a T-beam is only efficient when experiencing load from one side.
The different types of beams cut material in different areas based on how they expect to be loaded. So when thinking about parts in bending, remember these two things:
Now that we have discussed the basics of beam bending, this theory can be taken further by designing critical components, such as aircraft wings, ship masts, and even automotive chassis. Once a firm grasp is established, the possibilities of composites are almost endless!
Addcomposites is the provider of the Automated Fiber Placement (AFP) system. The AFP system can be rented on a monthly basis to work with thermosets, thermoplastic, dry fiber placement, or in combination with 3d printers.
Before getting to materials and settings that determine the strength of a part produced using ATL/AFP and composites, it is important to understand the physics and theory behind different aspects that affect its strength. In this section, we cover 3 concepts that lay the groundwork for strong ATL/AFP parts.
ATL/AFP parts are rarely 100% carbon fiber, as it is beneficial for cost and material savings to reinforce only the sections that experience the most force. This is why most composite parts are constructed more like sandwiches, with the outermost sections being the composite material and the internal structure being the core.
The core's main purpose is to increase the part to the desired thickness, without building it up with expensive carbon fiber. So, does the shell thickness or core density contribute more to part strength? The answer stems from the simple beam bending theory.
The key takeaway from beam bending theory is that the top and bottom surfaces of a beam experience the most force when bent, and we can optimize the strength of a beam for its weight by only adding material at these extremes, and using as little material as possible.
Say we have a simple beam, like a bridge, supported on both sides, and weight is centered between the end supports, as shown in the following diagram.
We can abstract this model to the 3 points of contact the beam experiences - one for the weight, and two for the supports. This forms a triangle, like so, where the contact points become the vertices.
When the weight applies a force to this beam, imagine the forces distributing along with this triangular structure. The two angled segments are compressed, and the horizontal segment gets loaded in tension.
The forces are distributed along the lengths of the triangle. The magnitude of the horizontal force ultimately depends on the thickness of the beam. As the beam gets thicker while the load remains constant, the base angles of the triangle increase, reducing the resultant horizontal force on the beam. When we increase the beam, like so, we can see the angle of force applied at the supports becomes more vertical:
As these angles increase, the resultant tensile force decreases. This means a thicker beam will be able to resist the bending tensile force of the weight much easier than a thinner beam. It is common sense that a thicker beam is able to support more weight than a thinner one, and this theory explains why.
A related aspect to beam bending theory describes that the largest loads on a bent beam are applied at its extremes. A bending force applied to a beam resolves to tensile and compressive forces on either side of what is called the "neutral axis", the plane in a beam at which no load is experienced.
In this case, the material below the neutral axis is loaded in tension and above the neutral axis is loaded in compression.
This information suggests that if optimizing a beam for its strength and weight, the material has the biggest impact on the top and bottom surfaces of the part, whereas the middle endures relatively little shearing forces.
Especially in ATL/AFP, tensile loads are more important and easier to optimize for than compressive loads, because each layer of fiber behaves like a strand (more on this later).
This explains why circular and box tubing, I-beams, and T-beams are so common in construction; they save weight by only adding material where the highest stresses are experienced. A circular tube can handle loading from all sides, because no matter where force is applied from, there are two "surfaces" at the extremes.
A box can handle loads from four sides because whichever side the load is applied from has an opposite side ready to experience tension. An I-beam however, is only capable of handling extreme force from two sides, and similarly, a T-beam is only efficient when experiencing load from one side.
The different types of beams cut material in different areas based on how they expect to be loaded. So when thinking about parts in bending, remember these two things:
Now that we have discussed the basics of beam bending, this theory can be taken further by designing critical components, such as aircraft wings, ship masts, and even automotive chassis. Once a firm grasp is established, the possibilities of composites are almost endless!
Addcomposites is the provider of the Automated Fiber Placement (AFP) system. The AFP system can be rented on a monthly basis to work with thermosets, thermoplastic, dry fiber placement, or in combination with 3d printers.