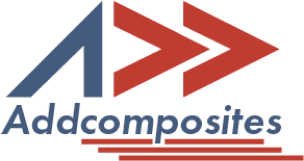
In the evolving landscape of composite manufacturing, filament winding has established itself as a crucial technique for producing high-performance structures. However, not all filament winding systems are created equal. The ADD Filament Winding System represents a significant advancement in this technology, offering unprecedented versatility that goes beyond traditional winding capabilities.
Traditional filament winding is typically limited to axially symmetric shapes such as tubes, ducts, and pressure vessels. The simplest two-axis winders control only the rotation of the mandrel and the transverse movement of the conveying unit, making them suitable only for producing reinforced pipes and tubes11. Even the more advanced four-axis machines, while capable of producing pressure vessels, still operate within significant constraints11.
In contrast, the ADD Filament Winding System breaks free from these limitations through innovative design and advanced control systems. Unlike conventional systems that often require frequent operator intervention during various winding operations (significantly impacting productivity)11, the ADD system offers a higher degree of automation and precision.
The ADD Filament Winding System excels in its ability to create diverse winding patterns, offering designers unprecedented freedom to optimize structures for specific applications.
The system's AddWinding module enables a variety of winding features including:
This flexibility allows engineers to create structures with tailored mechanical properties. For instance, a high angle "hoop" winding provides superior circumferential strength, while lower angle patterns (either polar or helical) deliver greater longitudinal/axial tensile strength3.
What truly sets the ADD system apart is its precise control over critical process parameters:
The system allows for semi-geodesic winding, which increases design freedom and enables the winding of previously unwindable shapes or the incorporation of load-distributing inserts1.
The ADD Filament Winding System offers several capabilities that distinguish it from conventional systems on the market.
Perhaps the most revolutionary aspect of the ADD system is its ability to function as both an Automated Fiber Placement (AFP) system and a filament winding system. This dual-mode operation allows manufacturers to leverage the strengths of each method as needed5.
The system can perform precise, non-geodesic fiber placement like traditional AFP while also achieving high-speed winding for cylindrical sections. This adaptability makes it ideal for producing complex components with varying geometrical features5.
The ADD system handles a wide range of materials, including:
This material flexibility accommodates various design requirements and enables the production of components with optimized performance characteristics5.
Incorporating cutting-edge sensing technologies, the ADD system offers:
These features ensure consistent quality and reduce waste by identifying potential issues before they affect the final product.
The versatility of the ADD Filament Winding System makes it suitable for a wide range of applications across multiple industries.
With the growing demand for hydrogen storage solutions, the ADD system's ability to create optimized pressure vessels is particularly valuable. The automotive sector has increasing demand for both low-pressure vessels for natural gas storage (35 MPa) and high-pressure vessels (70 MPa) for hydrogen and compressed natural gas storage8.
The aerospace industry benefits from the system's precision and ability to create lightweight, high-strength components. Applications include missile casings, rocket motor cases, and aircraft fuselages8, where weight optimization and structural integrity are paramount.
The ADD system excels in producing complex pipe fittings for the chemical and oil industries. Its advanced CNC capabilities enable automated production of non-axisymmetric shapes that would be challenging or impossible with traditional winding equipment8.
From golf club shafts to masts for windsurfing, the ADD system can create high-performance sporting goods with precisely tailored mechanical properties13. The ability to vary wall thickness and fiber angle along the length of a tube allows for optimized performance characteristics.
The ADD Filament Winding System represents the next evolution in composite manufacturing technology. By combining the precision of AFP with the efficiency of filament winding, it offers manufacturers unprecedented versatility and control.
As industries continue to demand lighter, stronger, and more complex composite structures, systems like ADD that break free from traditional limitations will become increasingly valuable. The ability to optimize both shape and lay-up, combined with advanced automation and process control, positions the ADD Filament Winding System at the forefront of composite manufacturing technology.
For manufacturers looking to expand their capabilities beyond traditional filament winding, the ADD system offers a pathway to new applications, improved efficiency, and enhanced product performance.