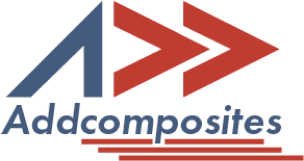
A digital twin can be defined as a virtual replica of the product. It starts as a 3D model that is similar to the physical version of the product. The main characteristic of a digital twin is that it allows analyzing real-world data and real-time monitoring of the physical product even after it has left the factory, and it is operating in the field.
The data is collected by means of sensors on the physical version of the product and it is then sent to the digital twin to study the behavior of the physical twin. By using this practice, it is possible to:
Due to the complexity of the production process safety margins need to be included in the mechanical design of such parts, which in turn offsets some of the advantages of lightweight components. Better documentation of the production process and real world part monitoring will lead to better manufacturing practices, with the potential to keep the safety margins within reasonable ranges while enabling more efficient defect handling and rework processes. While AFP processes have been taking an important place in manufacturing, they have been restricted to a niche industry. However, with the advent of the AFP-XS plug-n-produce solution, it is now possible to cost-effectively implement digital twins in your production line.
The cost of the sensor suite and communication is continuously decreasing, the investment in the infrastructure to realize a digital twin is becoming especially interesting because the costs of the parts produced are relatively high and monitoring of parts pays off quickly. Furthermore, substantial savings may be achieved due to a reduction in end-of-line testing. Therefore, the interest in the implementation of digital twins is the highest it's ever been. The digital twin implemented and proven in Aerospace applications can be scaled to achieve economies of scale, thus making it accessible to other industries employing similar techniques.
During the lay-up process a number of variations and defects may occur, that include e.g. gaps or overlaps in the material, distortions of the fabric, wrinkles, or any kind of foreign objects. A few examples are shown in the figure below. The detection of the defects is very often done through human inspection after each layer and in recent times through sensors.
Figure: Various kinds of defects, such as wrinkles, early cut tapes, foreign objects (top row), and large gaps (bottom row)
The various kinds of defects can be detected by two different modalities:
Each feature (defect) can have a measured value (manufactured in the database structure) and a simulated value (simulated). These numerical results are classified into three types:
The simulation software is continuously pulling these data and as soon as it receives the information that the defect data are complete, it will start the processing. The initial processing will be done through the analytical model to quickly obtain a first estimate about the margin of safety. A detailed finite-element calculation is done only for critical defects that require deeper analysis. The whole process is repeated for each ply, i.e. simulation,
decision making and re-work take place after each ply!
For the experiments done in the paper titled "A digital twin for composite parts manufacturing", a modular version of the FScan (fiber orientation measurement) and LScan (depth data) sensor was used to cover the whole width of the material in an Automated Dry Fiber Placement process, where unidirectional non-crimp-fabric was placed on a slightly curved part. The figure below indicates the area covered by the sensor during this particular scanning pass
Figure: Features representing ply boundaries and gap back-projected onto the surface of the manufactured part.
The main conclusions from the experiments are that it is possible to collect all relevant information needed for setting up a digital twin of a composite part in real-time and during the production process. The impact of the defects can be calculated in (almost) real-time using an analytical model and only in the case of critical defects a finite-element model is needed.
Based on the experiment it seems finally manufacturers can take advantage by collecting all relevant information needed for setting up a digital twin of a composite part in real-time and during the production process. This allows solidifying continuous manufacturing operations as original components can be easily accessed whenever they are required.
this information combined with machine learning and big data can provide the following benefits:
A digital twin can be defined as a virtual replica of the product. It starts as a 3D model that is similar to the physical version of the product. The main characteristic of a digital twin is that it allows analyzing real-world data and real-time monitoring of the physical product even after it has left the factory, and it is operating in the field.
The data is collected by means of sensors on the physical version of the product and it is then sent to the digital twin to study the behavior of the physical twin. By using this practice, it is possible to:
Due to the complexity of the production process safety margins need to be included in the mechanical design of such parts, which in turn offsets some of the advantages of lightweight components. Better documentation of the production process and real world part monitoring will lead to better manufacturing practices, with the potential to keep the safety margins within reasonable ranges while enabling more efficient defect handling and rework processes. While AFP processes have been taking an important place in manufacturing, they have been restricted to a niche industry. However, with the advent of the AFP-XS plug-n-produce solution, it is now possible to cost-effectively implement digital twins in your production line.
The cost of the sensor suite and communication is continuously decreasing, the investment in the infrastructure to realize a digital twin is becoming especially interesting because the costs of the parts produced are relatively high and monitoring of parts pays off quickly. Furthermore, substantial savings may be achieved due to a reduction in end-of-line testing. Therefore, the interest in the implementation of digital twins is the highest it's ever been. The digital twin implemented and proven in Aerospace applications can be scaled to achieve economies of scale, thus making it accessible to other industries employing similar techniques.
During the lay-up process a number of variations and defects may occur, that include e.g. gaps or overlaps in the material, distortions of the fabric, wrinkles, or any kind of foreign objects. A few examples are shown in the figure below. The detection of the defects is very often done through human inspection after each layer and in recent times through sensors.
Figure: Various kinds of defects, such as wrinkles, early cut tapes, foreign objects (top row), and large gaps (bottom row)
The various kinds of defects can be detected by two different modalities:
Each feature (defect) can have a measured value (manufactured in the database structure) and a simulated value (simulated). These numerical results are classified into three types:
The simulation software is continuously pulling these data and as soon as it receives the information that the defect data are complete, it will start the processing. The initial processing will be done through the analytical model to quickly obtain a first estimate about the margin of safety. A detailed finite-element calculation is done only for critical defects that require deeper analysis. The whole process is repeated for each ply, i.e. simulation,
decision making and re-work take place after each ply!
For the experiments done in the paper titled "A digital twin for composite parts manufacturing", a modular version of the FScan (fiber orientation measurement) and LScan (depth data) sensor was used to cover the whole width of the material in an Automated Dry Fiber Placement process, where unidirectional non-crimp-fabric was placed on a slightly curved part. The figure below indicates the area covered by the sensor during this particular scanning pass
Figure: Features representing ply boundaries and gap back-projected onto the surface of the manufactured part.
The main conclusions from the experiments are that it is possible to collect all relevant information needed for setting up a digital twin of a composite part in real-time and during the production process. The impact of the defects can be calculated in (almost) real-time using an analytical model and only in the case of critical defects a finite-element model is needed.
Based on the experiment it seems finally manufacturers can take advantage by collecting all relevant information needed for setting up a digital twin of a composite part in real-time and during the production process. This allows solidifying continuous manufacturing operations as original components can be easily accessed whenever they are required.
this information combined with machine learning and big data can provide the following benefits: