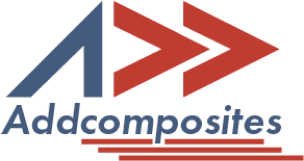
Welcome to our deep dive into the world of filament winding technology – a game-changer in the manufacturing of composite structures. Before we delve into the intricate details, here's a quick overview of what you'll discover in this comprehensive blog:
Filament winding technology offers significant advantages over traditional manufacturing methods. Its automated nature leads to increased precision and consistency in production, which is crucial for high-performance applications. Unlike conventional methods that can be labor-intensive and error-prone, filament winding allows for tighter quality control and uniformity in product characteristics. The process also enables the creation of complex shapes and structures that would be challenging or impossible to achieve with traditional manufacturing.
The advancement in composite materials has been a pivotal factor in the popularity of filament winding. Composite materials, known for their high strength-to-weight ratios, are ideal for filament winding. This technology effectively exploits the properties of composites, aligning fibers in specific directions to optimize strength and durability. Innovations in fiber materials and resin systems have further enhanced the performance of filament-wound products, leading to broader applications and improved material properties.
Filament winding has found extensive applications in various industries, notably aerospace and automotive. In aerospace, the technology is used to manufacture components like fuel tanks, fuselage sections, and engine parts, where weight reduction and strength are paramount. The automotive industry benefits from the lightweight and strong components that filament winding can produce, contributing to fuel efficiency and safety. Other industries, including renewable energy, sports equipment, and infrastructure, have also adopted filament winding for its versatility and efficiency.
Filament winding is an automated process of wrapping fiber filaments soaked in resin around a mandrel, typically used for creating cylindrical structures. The process is highly efficient in optimizing the anisotropic properties of the fibers, making it ideal for high-strength applications.
The evolution from mechanical to computer-controlled winding machines has enhanced precision, allowing for more complex shapes. Advanced technologies, like Automated Fiber Placement (AFP) and Structural Continuous Fiber 3D (SCF3D) Printing, have further expanded its capabilities.
Winding patterns, such as geodesic and non-geodesic, significantly impact the product's properties. The choice of materials – glass, carbon, or aramid fibers, combined with various resin systems – is crucial in determining the strength and functionality of the final product.
Critical parameters like fiber tension, winding angle, and speed are meticulously controlled to ensure quality and consistency in the filament-wound products.
Filament winding technology has a broad spectrum of applications, contributing significantly to various industries with its unique capabilities.
A primary application is in creating composite pressure vessels and pipes. These structures, made with filament winding, offer high strength-to-weight ratios and corrosion resistance, essential for consistent performance under internal pressure.
The technology enhances the low-velocity impact resistance of structures like prestressed functionally graded hybrid pipes. This is crucial in applications where structures are subjected to dynamic loads, ensuring durability and longevity.
In the oil and gas sector, filament winding is pivotal in manufacturing composite pipes. Research indicates that the drilling performance and damage resistance of these pipes can be significantly improved through optimized winding patterns and material choices.
With the rise of electric vehicles, filament winding is increasingly used to produce motor sleeves. These sleeves must withstand high tension and heat, making the precise fiber alignment and material properties achievable through filament winding ideal for EV motor applications. The technology’s ability to tailor motor sleeves to specific performance requirements further underscores its value in the burgeoning EV industry.
Filament winding technology significantly enhances production efficiency and product performance across various industries, as highlighted in the "Application of Filament Winding Technology in Composite Pressure Vessels and Challenges - A Review" document.
Filament winding is instrumental in manufacturing products for a wide range of applications, including:
One of the key benefits of filament winding in the transportation sector, particularly with natural gas vehicles (NGVs), is the substantial weight reduction achieved using Type 4 composite pressure vessels (CPVs). This reduction (around 75%) directly translates to improved fuel efficiency and lower operating costs.
Filament winding technology allows for flexibility in designing products to withstand various environmental conditions, including thermal loading. This adaptability is crucial for products like CPVs in cryogenic applications, where the composite materials must maintain their mechanical properties at low temperatures.
While filament winding offers numerous advantages, the technology continues to evolve. Ongoing research and development are necessary to further reduce costs and improve the efficiency, reliability, and durability of filament-wound products, paving the way for extended commercial implementations.
Filament winding technology, as explored in the reviewed documents, presents a transformative approach in the manufacturing of composite structures, offering unique benefits across various industries. This technology stands out for its ability to create high-strength, lightweight components, crucial in aerospace, automotive, and renewable energy sectors.
As we look forward, filament winding is poised to play an even more significant role in various sectors, driven by advancements in materials science and manufacturing technologies. Its application in emerging fields, particularly in renewable energy and electric vehicles, is expected to grow, reflecting the technology's adaptability and relevance in an evolving industrial landscape.
We extend our heartfelt thanks to the authors of the paper "Application of Filament Winding Technology in Composite Pressure Vessels and Challenges - A Review." Their comprehensive research and insightful analysis have been instrumental in the creation of this blog. Their dedication to exploring filament winding technology has provided invaluable information and understanding, which we have had the privilege to share with our readers. Their contributions to the field are deeply appreciated and have greatly enriched our discussion on this cutting-edge technology.
Discover the future of composite manufacturing with Addcomposites! Here's how you can get involved:
At Addcomposites, we are dedicated to revolutionizing composite manufacturing. Our AFP systems and comprehensive support services are waiting for you to harness. So, don't wait – get started on your journey to the future of manufacturing today!
Welcome to our deep dive into the world of filament winding technology – a game-changer in the manufacturing of composite structures. Before we delve into the intricate details, here's a quick overview of what you'll discover in this comprehensive blog:
Filament winding technology offers significant advantages over traditional manufacturing methods. Its automated nature leads to increased precision and consistency in production, which is crucial for high-performance applications. Unlike conventional methods that can be labor-intensive and error-prone, filament winding allows for tighter quality control and uniformity in product characteristics. The process also enables the creation of complex shapes and structures that would be challenging or impossible to achieve with traditional manufacturing.
The advancement in composite materials has been a pivotal factor in the popularity of filament winding. Composite materials, known for their high strength-to-weight ratios, are ideal for filament winding. This technology effectively exploits the properties of composites, aligning fibers in specific directions to optimize strength and durability. Innovations in fiber materials and resin systems have further enhanced the performance of filament-wound products, leading to broader applications and improved material properties.
Filament winding has found extensive applications in various industries, notably aerospace and automotive. In aerospace, the technology is used to manufacture components like fuel tanks, fuselage sections, and engine parts, where weight reduction and strength are paramount. The automotive industry benefits from the lightweight and strong components that filament winding can produce, contributing to fuel efficiency and safety. Other industries, including renewable energy, sports equipment, and infrastructure, have also adopted filament winding for its versatility and efficiency.
Filament winding is an automated process of wrapping fiber filaments soaked in resin around a mandrel, typically used for creating cylindrical structures. The process is highly efficient in optimizing the anisotropic properties of the fibers, making it ideal for high-strength applications.
The evolution from mechanical to computer-controlled winding machines has enhanced precision, allowing for more complex shapes. Advanced technologies, like Automated Fiber Placement (AFP) and Structural Continuous Fiber 3D (SCF3D) Printing, have further expanded its capabilities.
Winding patterns, such as geodesic and non-geodesic, significantly impact the product's properties. The choice of materials – glass, carbon, or aramid fibers, combined with various resin systems – is crucial in determining the strength and functionality of the final product.
Critical parameters like fiber tension, winding angle, and speed are meticulously controlled to ensure quality and consistency in the filament-wound products.
Filament winding technology has a broad spectrum of applications, contributing significantly to various industries with its unique capabilities.
A primary application is in creating composite pressure vessels and pipes. These structures, made with filament winding, offer high strength-to-weight ratios and corrosion resistance, essential for consistent performance under internal pressure.
The technology enhances the low-velocity impact resistance of structures like prestressed functionally graded hybrid pipes. This is crucial in applications where structures are subjected to dynamic loads, ensuring durability and longevity.
In the oil and gas sector, filament winding is pivotal in manufacturing composite pipes. Research indicates that the drilling performance and damage resistance of these pipes can be significantly improved through optimized winding patterns and material choices.
With the rise of electric vehicles, filament winding is increasingly used to produce motor sleeves. These sleeves must withstand high tension and heat, making the precise fiber alignment and material properties achievable through filament winding ideal for EV motor applications. The technology’s ability to tailor motor sleeves to specific performance requirements further underscores its value in the burgeoning EV industry.
Filament winding technology significantly enhances production efficiency and product performance across various industries, as highlighted in the "Application of Filament Winding Technology in Composite Pressure Vessels and Challenges - A Review" document.
Filament winding is instrumental in manufacturing products for a wide range of applications, including:
One of the key benefits of filament winding in the transportation sector, particularly with natural gas vehicles (NGVs), is the substantial weight reduction achieved using Type 4 composite pressure vessels (CPVs). This reduction (around 75%) directly translates to improved fuel efficiency and lower operating costs.
Filament winding technology allows for flexibility in designing products to withstand various environmental conditions, including thermal loading. This adaptability is crucial for products like CPVs in cryogenic applications, where the composite materials must maintain their mechanical properties at low temperatures.
While filament winding offers numerous advantages, the technology continues to evolve. Ongoing research and development are necessary to further reduce costs and improve the efficiency, reliability, and durability of filament-wound products, paving the way for extended commercial implementations.
Filament winding technology, as explored in the reviewed documents, presents a transformative approach in the manufacturing of composite structures, offering unique benefits across various industries. This technology stands out for its ability to create high-strength, lightweight components, crucial in aerospace, automotive, and renewable energy sectors.
As we look forward, filament winding is poised to play an even more significant role in various sectors, driven by advancements in materials science and manufacturing technologies. Its application in emerging fields, particularly in renewable energy and electric vehicles, is expected to grow, reflecting the technology's adaptability and relevance in an evolving industrial landscape.
We extend our heartfelt thanks to the authors of the paper "Application of Filament Winding Technology in Composite Pressure Vessels and Challenges - A Review." Their comprehensive research and insightful analysis have been instrumental in the creation of this blog. Their dedication to exploring filament winding technology has provided invaluable information and understanding, which we have had the privilege to share with our readers. Their contributions to the field are deeply appreciated and have greatly enriched our discussion on this cutting-edge technology.
Discover the future of composite manufacturing with Addcomposites! Here's how you can get involved:
At Addcomposites, we are dedicated to revolutionizing composite manufacturing. Our AFP systems and comprehensive support services are waiting for you to harness. So, don't wait – get started on your journey to the future of manufacturing today!