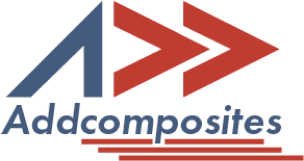
Robotic filament winding presents an advanced avenue for creating high-performance materials, particularly in industries like aerospace, automotive, and construction. The core technology involves winding fibers around shapes to enhance structural integrity and minimize material use. Yet, transitioning from traditional methodologies to a more complex 3D robotic filament winding introduces significant challenges.
traditional filament winding has the following limitations that make it unsuitable for modern challenges:
In contrast, coreless robotic winding (CRW) allows for greater design freedom and the creation of complex, 3D-reinforced structures without the need for a core.
Modern engineering approaches address the limitations of traditional filament winding techniques in the following ways:
By leveraging these modern engineering approaches, the limitations of traditional filament winding techniques can be overcome, enabling the production of complex, load-optimized composite structures for various applications in aerospace, automotive, and civil engineering.
The path planning process using Hierholzer's algorithm and 3D geometric considerations can be broken down into two main steps:
By combining Hierholzer's algorithm for node sequence generation and 3D geometric considerations for spatial path planning, the proposed approach enables the automated and optimized winding of complex, load-adapted composite structures using coreless robotic winding techniques.
Automating the 3D robotic filament winding process with improved algorithms enhances efficiency and precision in composite manufacturing in several ways:
By leveraging improved algorithms for 3D robotic filament winding, manufacturers can enhance efficiency, precision, and overall performance in composite manufacturing, ultimately leading to the production of high-quality, load-optimized structures for a wide range of applications.
we'd like to extend our gratitude to Johannes Mersch, Danny Friese, and Hung Le Xuan, the esteemed authors of the PDF titled "Automating the 3D robotic filament winding process for high-performance composite materials." Their pioneering research and insightful contributions have been instrumental in crafting this blog, providing a deep dive into the complexities and innovations within the field of robotic filament winding. Their dedication to advancing this technology not only enhances our understanding but also pushes the boundaries of what is possible in composite manufacturing. Thank you, Johannes, Danny, and Hung, for your significant contributions to this exciting field!
Discover the future of composite manufacturing with Addcomposites! Here's how you can get involved:
At Addcomposites, we are dedicated to revolutionizing composite manufacturing. Our AFP systems and comprehensive support services are waiting for you to harness. So, don't wait – get started on your journey to the future of manufacturing today!
Robotic filament winding presents an advanced avenue for creating high-performance materials, particularly in industries like aerospace, automotive, and construction. The core technology involves winding fibers around shapes to enhance structural integrity and minimize material use. Yet, transitioning from traditional methodologies to a more complex 3D robotic filament winding introduces significant challenges.
traditional filament winding has the following limitations that make it unsuitable for modern challenges:
In contrast, coreless robotic winding (CRW) allows for greater design freedom and the creation of complex, 3D-reinforced structures without the need for a core.
Modern engineering approaches address the limitations of traditional filament winding techniques in the following ways:
By leveraging these modern engineering approaches, the limitations of traditional filament winding techniques can be overcome, enabling the production of complex, load-optimized composite structures for various applications in aerospace, automotive, and civil engineering.
The path planning process using Hierholzer's algorithm and 3D geometric considerations can be broken down into two main steps:
By combining Hierholzer's algorithm for node sequence generation and 3D geometric considerations for spatial path planning, the proposed approach enables the automated and optimized winding of complex, load-adapted composite structures using coreless robotic winding techniques.
Automating the 3D robotic filament winding process with improved algorithms enhances efficiency and precision in composite manufacturing in several ways:
By leveraging improved algorithms for 3D robotic filament winding, manufacturers can enhance efficiency, precision, and overall performance in composite manufacturing, ultimately leading to the production of high-quality, load-optimized structures for a wide range of applications.
we'd like to extend our gratitude to Johannes Mersch, Danny Friese, and Hung Le Xuan, the esteemed authors of the PDF titled "Automating the 3D robotic filament winding process for high-performance composite materials." Their pioneering research and insightful contributions have been instrumental in crafting this blog, providing a deep dive into the complexities and innovations within the field of robotic filament winding. Their dedication to advancing this technology not only enhances our understanding but also pushes the boundaries of what is possible in composite manufacturing. Thank you, Johannes, Danny, and Hung, for your significant contributions to this exciting field!
Discover the future of composite manufacturing with Addcomposites! Here's how you can get involved:
At Addcomposites, we are dedicated to revolutionizing composite manufacturing. Our AFP systems and comprehensive support services are waiting for you to harness. So, don't wait – get started on your journey to the future of manufacturing today!